Every business must prioritize quality management to guarantee that its goods and services either meet or surpass the expectations of its customers.
Odoo 17, a comprehensive enterprise resource planning (ERP) software, allows quality management to be seamlessly integrated into work orders, increasing efficiency and customer satisfaction.
This blog discusses the importance of quality management in work orders and provides a detailed process for implementing it in Odoo 17.
Quality management in work orders is carefully monitoring and managing the processes involved in manufacturing or delivering goods and services.
It includes actions such as quality planning, assurance, and quality control to verify that each work order follows predetermined standards and requirements.
The Significance of Quality Management in Work Orders:
Customer Satisfaction: Consistent delivery of high-quality products or services increases client satisfaction and loyalty.
Cost Reduction: Effective quality management reduces rework, waste, defects, resulting in cost savings.
Compliance: Following quality standards and regulations assures legal compliance and reduces risk.
Continuous Improvement: By identifying fields for improvement, quality management promotes a culture of continuous improvement in processes and products.
Quality checks are manual inspections performed by staff to ensure product quality. Within Odoo, these checks can be performed on individual products or multiple products within the same inventory activity or production order.
A Quality Control Point (QCP) can automatically generate quality checks at predetermined intervals. These checks are effortlessly integrated into manufacturing or inventory orders, urging staff who process the orders to comply with them.
Although Quality Control Points (QCPs) often automate the development of quality checks, it is also possible to generate a single quality check manually.
This manual approach is useful when an employee needs to plan a one-time quality check or document an unprompted quality inspection they performed.
To manually create a single quality check, follow these steps:
1. Go to Quality ? Quality Control ? Quality checks.
2. Click "New" to start a fresh quality check.
3. On the quality check form, begin by selecting an option from the "Control per" drop-down box. When manually establishing a quality check, you'll see three possibilities in the "Control per" drop-down menu:
Operation: This option demands a quality check for the entire activity, such as a delivery order, which includes all products.
Product: Selecting this option initiates a quality check for each unit of a product engaged in the activity, such as every unit in a delivery order.
Quantity: Selecting this option triggers a quality check for each quantity of a product in the process. For example, if a delivery order includes five units of a product, five quality checks will be performed.
Additionally, selecting "Quantity" will bring up a Lot/Serial drop-down field. Here, you can provide the lot or serial number for which the quality check should be performed.
4. After selecting the "Control per" option, select an inventory activity from the "Picking" or "Production Order" drop-down menus. This step is necessary because Odoo 17 ERP requires information about the exact operation for which the quality check is performed.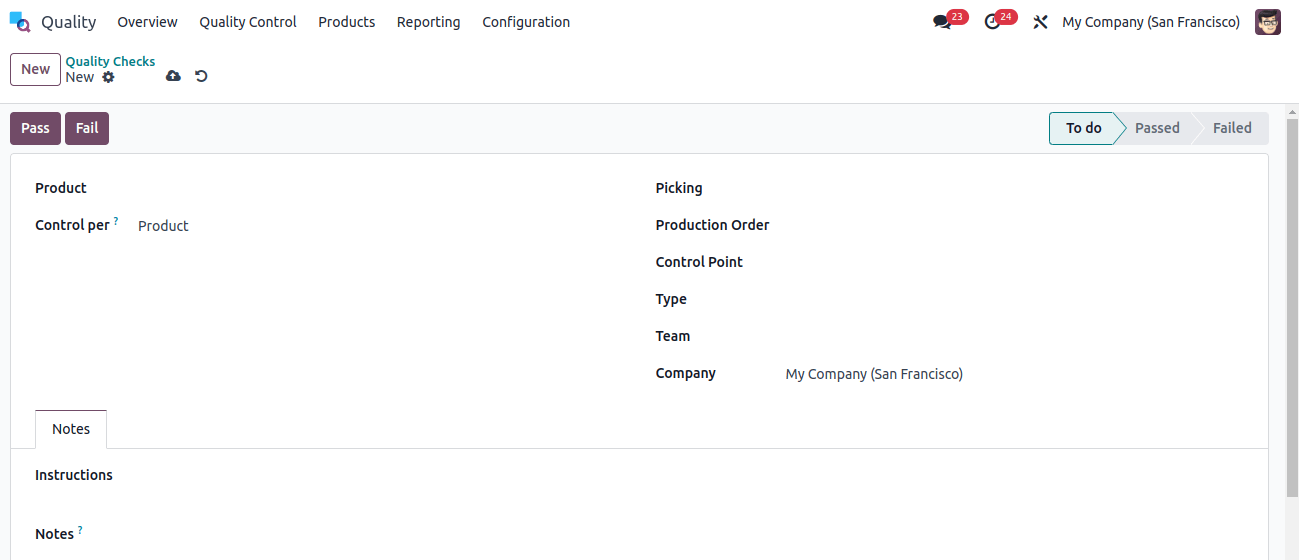
5. If the quality check must be associated with a specific Quality Control Point (QCP), pick it from the "Control Point" drop-down menu.
This option is useful when manually establishing a quality check that must be identified as belonging to a specific QCP.
6. Now select a quality check type from the "Type" drop-down field:
Instructions: It also includes detailed instructions on how to execute the quality check.
Take a Picture: It also requires that a photo be attached to the check before it can be performed.
Pass-Fail: Use this type when the product being tested must meet specified criteria to pass the check.
Measure: Selecting this kind opens an input field where you can enter a measurement before finishing the check.
7. In the "Team" section, select the quality team in charge of the quality check. Then, in the "Company" field, pick the firm that owns the product under inspection.
8. The "Notes" tab, placed near the bottom of the form, contains two text entry boxes.
In the "Instructions" box, enter any specific quality inspection instructions (for example, "Attach a picture of the product").
In the "Notes" box, enter pertinent information regarding the quality check, such as who generated it and why.
9. In this case, you've selected a manufacturing order (MO) that includes a work order requiring a quality check.
This means that during the production process, a specific step or task in the work order must be quality verified to guarantee conformity with standards or requirements.
If the quality check is being conducted instantly, you can take action by clicking the "Pass" button in the upper left corner of the screen if the check passes and the "Fail" button. This enables fast feedback and action based on the results of the quality check.
Quality Check on Work Order
To do a quality check on a work order, navigate to Manufacturing. Operations? Manufacturing orders. From there, choose the manufacturing order (MO) that includes the applicable work order that requires a quality check.
This allows you to view the specifics of the manufacturing order and start the quality inspection for the corresponding work order.
Click the "Open Work Order" button (external link icon) next to the applicable work order.
To access the Shop Floor module, locate and click the "Open Shop Floor" button in the Work Orders pop-up window that follows.
With these steps, you can easily switch to the shop floor module and complete the quality check for the selected work order.
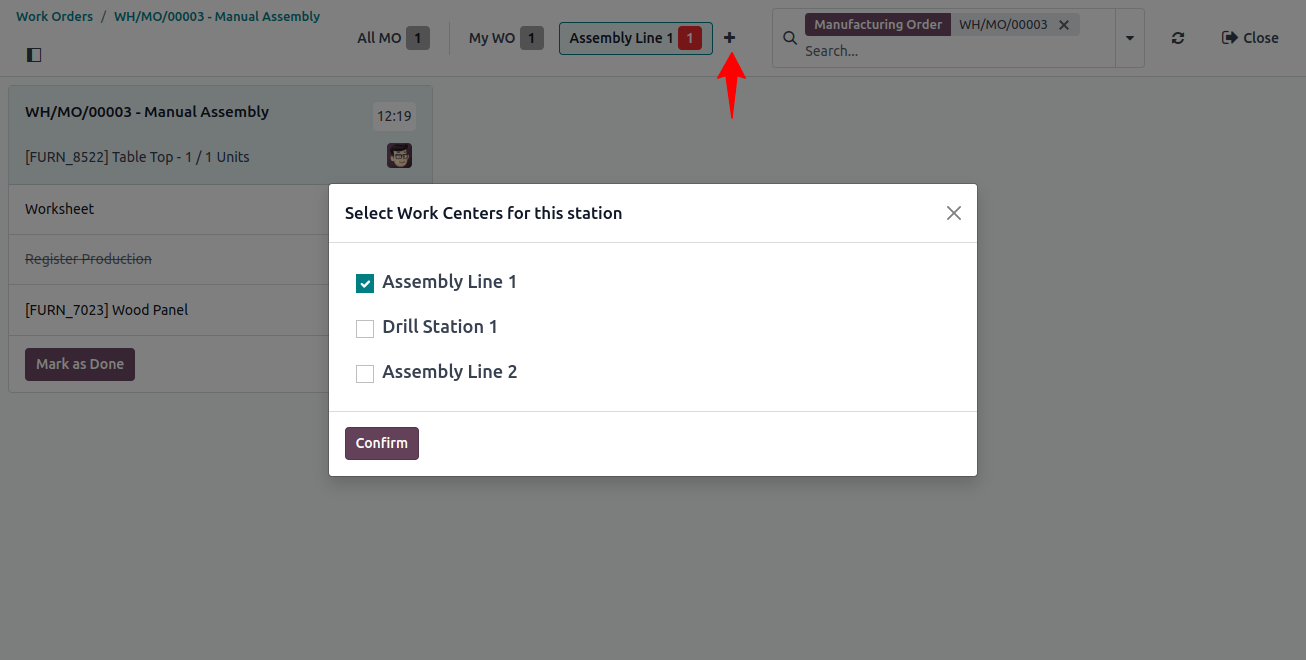
When accessed from a specific work order, the shop floor module takes you to the page for the assigned work center where the order is scheduled to be processed.
Follow these instructions to complete the work order's up to the quality check step. Continue the work order processes until you get to the quality check step. Clicking on the step will reveal a pop-up window with thorough instructions on how to finish the check.
Follow the instructions carefully. If the quality check is a Pass-Fail kind, click either the "Pass" or "Fail" button based on the results.
After completing each step correctly, click the "Validate" button to finalize the quality check.
In addition, you can complete a quality check by clicking the button on the right side of the step. This operation automatically stamps the check as "Passed" without further confirmation.
Effective quality management is important to the success and sustainability of any corporate operation.
Implementing a disciplined approach to quality control in work orders with Odoo 17 can help businesses improve product quality, customer satisfaction, and overall operational efficiency.
Businesses may remain competitive in today’s changing industry by consistently monitoring, reviewing, and improving their quality practices.